- HOME
- Products
- Wear Resistant Materials
- Coal-Fired Power Generation Products and Solutions
- Mining Industry Products and Solutions
- Cement Industry Products and Solutions
- Steel Industry Products and Solutions
- Asphalt Industry Products and Solutions
- Aggregate Industry Products and Solutions
- Dredging Industry Products and Solutions
- Foundry Industry Products and Solutions
- Metal Recycling Industry Products and Solutions
- Pulp and Paper Industry Products and Solutions
- Sugar Cane Processing Industry Products and Solutions
- Services
- Contact
- About
- News
- Careers
- Blog
- Terms
Patented Rotating Vane Wheel - CE HP / RP / RS Series Mill Modernization
Fine Tune Air Flows with the SAS Adjustable Throat
SAS Global has been building Rotating Vane Wheel Conversions for the CE Style Mill since the 1980's. The knowledge we gained from computer modeling and actual field-testing has allowed us to improve our design and enhance performance while still keeping the function of maintenance in mind. We strive to serve the operations side, with performance, and also provide maintenance with a product that has wear resistant material options, which can be tailored to the particular fuel the plant is burning. The proven benefits of our Rotating Vane Wheel have been experienced by many Power Plants in North America and South with nearly 500 kits installed to date. Most plants, after installing and evaluating their first kit, have immediately scheduled all remaining mills to be converted to SAS vane wheels. Although not every plant has the same needs, listed below are a few reasons for installing our Patented Rotating Vane Wheel for the CE Style Mill.
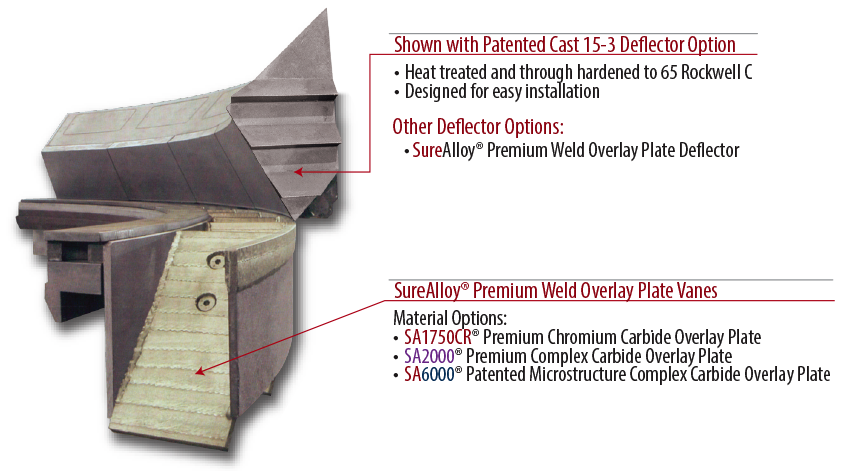
Shown above with closed race vane, also available in a cantilever vane configuration
PERFORMANCE BENEFITS:
- Lower Mill Motor Amps: Typical reductions have been 10% to 18%
- Lower Primary Air Flows: The SAS design has adjustable airport, allowing throat air velicities to be adjusted to match the required air mass
- Increased Fuel Drying Capability: The SAS vane/deflector arrangment dries the coal faster by providing a more evenly supported coal bed around the periphery of the bowl.
- Quicker Mill Response Time: An evenly supported coal bed and improved circulation/mixing of hot primary air provides smoother and quicker ramping of the mill.
- Increased Mill Capacity: Having extra capacity is beneficial should a mill be removed from service during peak generation times.
- Lower Maintenance Costs: Even coal flows at lower velocities will improve the life of internal mill components.
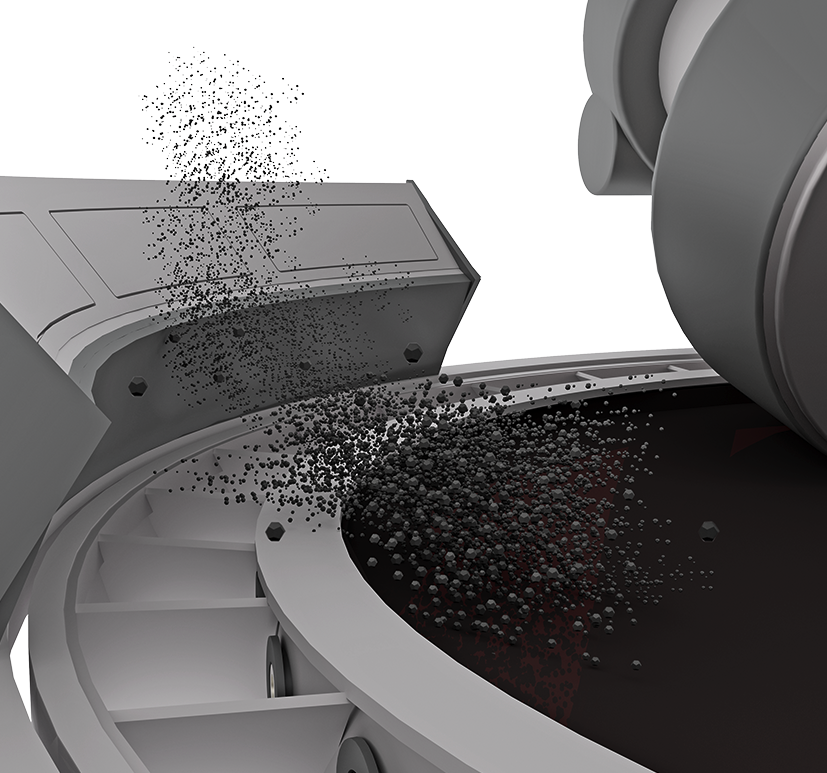
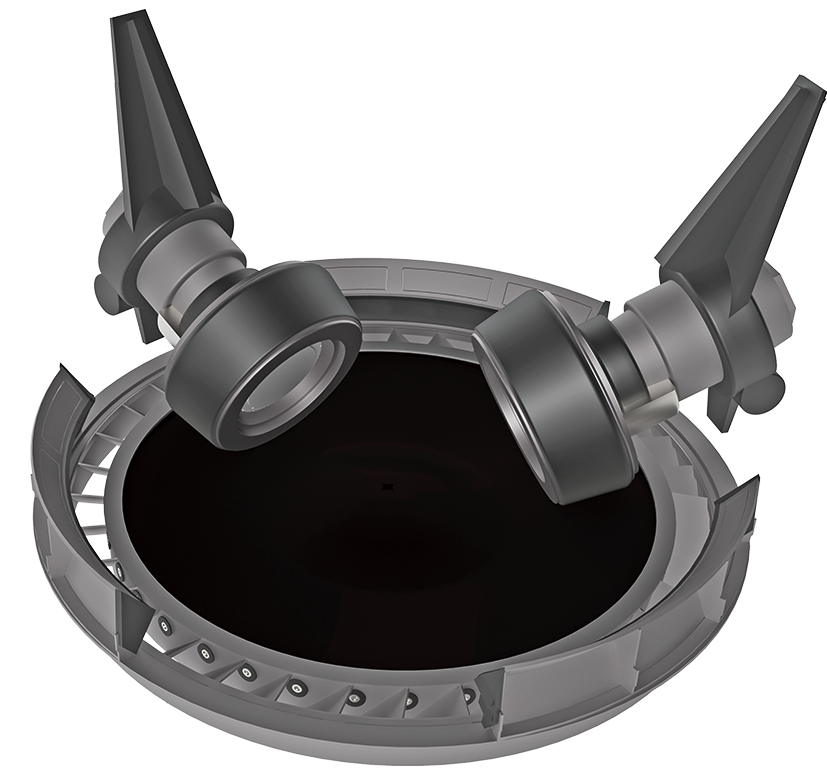
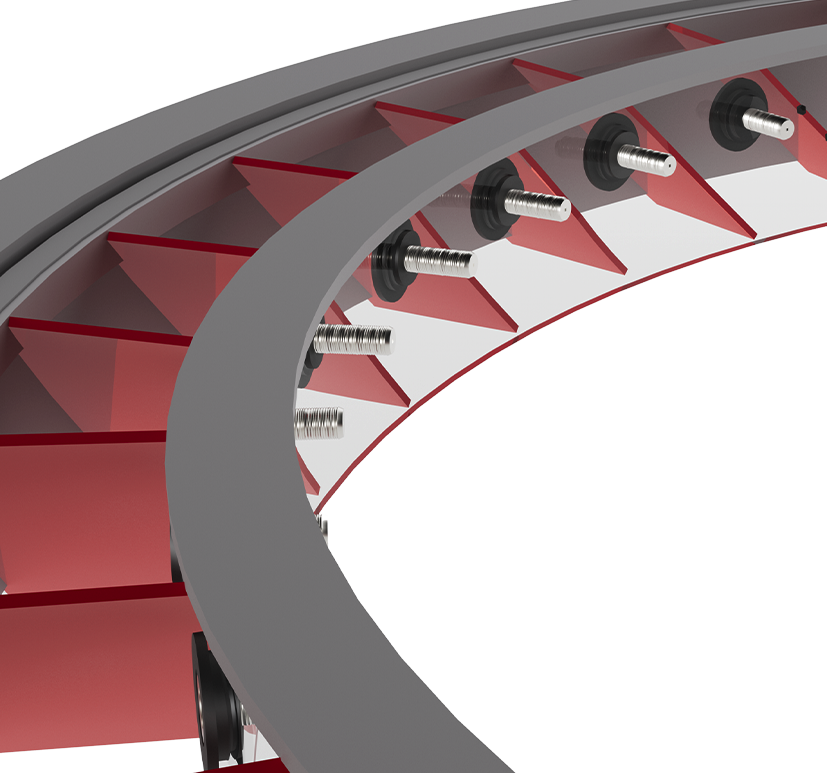
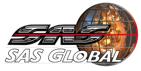
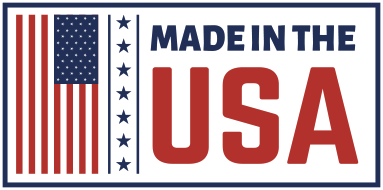
Copyright © 2024 SAS Global Corporation | All Rights Reserved