- HOME
- Products
- Wear Resistant Materials
- Coal-Fired Power Generation Products and Solutions
- Mining Industry Products and Solutions
- Cement Industry Products and Solutions
- Steel Industry Products and Solutions
- Asphalt Industry Products and Solutions
- Aggregate Industry Products and Solutions
- Dredging Industry Products and Solutions
- Foundry Industry Products and Solutions
- Metal Recycling Industry Products and Solutions
- Pulp and Paper Industry Products and Solutions
- Sugar Cane Processing Industry Products and Solutions
- Services
- Contact
- About
- News
- Careers
- Blog
- Terms
Other SAS Foundry Components
Increase Service Life • Increase Production • Reduce Maintenance • Reduce Downtime
Scalping Drums
One of the many products that we manufacture is a high performance - high quality Scalping Drum for the Wheelabrator® and Pangborn® shot blast machines.
SAS Global Corporation will custom build your Scalping Drum of carbon steel, alloy steel or 11% to 14% manganese steel. Our experienced engineering department will offer wear resistant material upgrades and operational enhancements to improve service life.
We also have the capability of rebuilding your worn Scalping Drums helping you reduce your maintenance expense by extending the life of your original equipment.
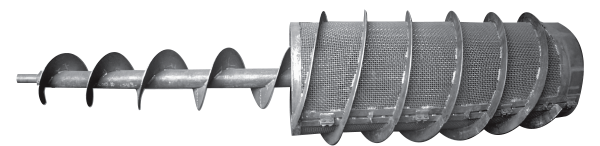
Wear Resistant Muller Bottoms
SAS Global manufactures high performance sand muller replacement bottoms. All of the parts manufactured by SAS are finished to exacting tolerances, which guarantees an accurate fit.
Key Features:
- SureAlloy Premium Carbide Overlay Plate provides an unsurpassed service life
- Top and bottom can be ground to insure they will lay flat, have a consistent thickness, and allow for a very accurate plow clearance
- SureAlloy Muller Bottoms outlast OEM cast bottoms and can be installed in less than half the time
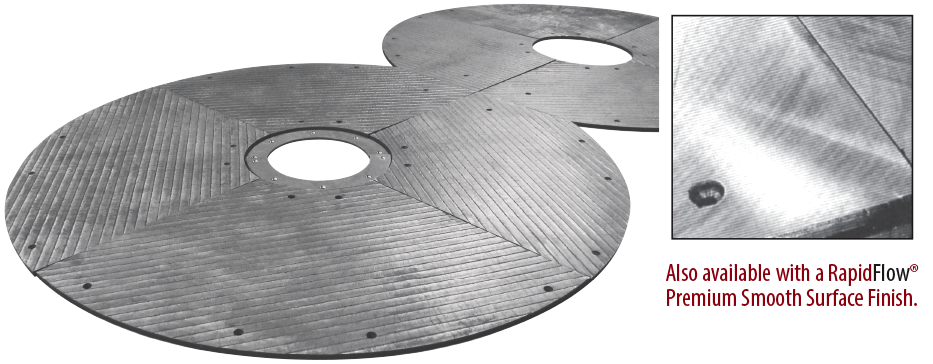
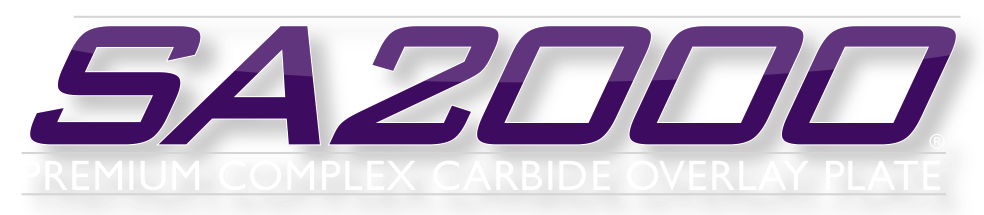
SA2000® is a specially formulated complex carbide overlay plate designed to generate a high concentration of small primary carbides greatly improving wear resistance over conventional chromium carbide alloys. The refined microstructure containing harder complex carbides provides greater wear resistance and improved toughness. The inert refractory carbides present also increase the temperature resistance and corrosion resistance. Up to double the service life of standard chromium carbide overlay plate.
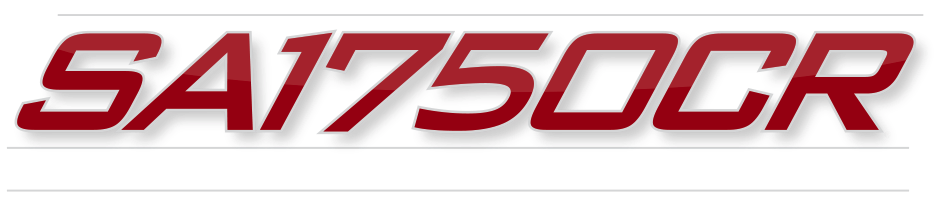
SA1750CR® is a Premium Chromium Carbide Overlay Plate consisting of a Hypereutectic Matrix with 50-60% Chromium Carbides metallurgically fused to an appropriate steel substrate. This large amount of hard chromium carbides allows SA1750CR to thrive in environments of extremely high abrasion.
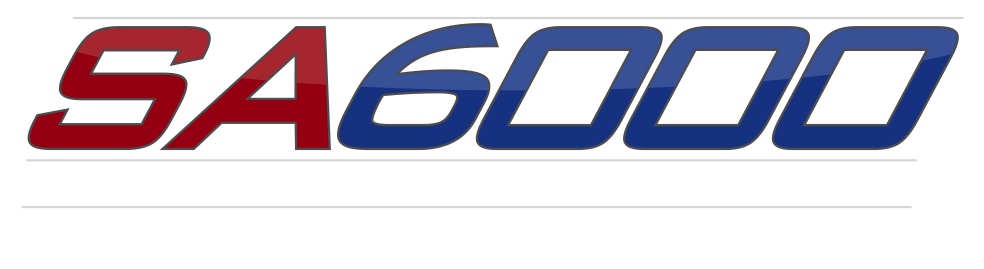
SA6000® is the new future of overlay wear plate. The patented microstructure of SA6000 is highly refined with tightly packed complex carbides. This fine grain microstructure reduces the propagation of cracks, which results in not only superior protection from abrasion, but also unheard of impact resistance!
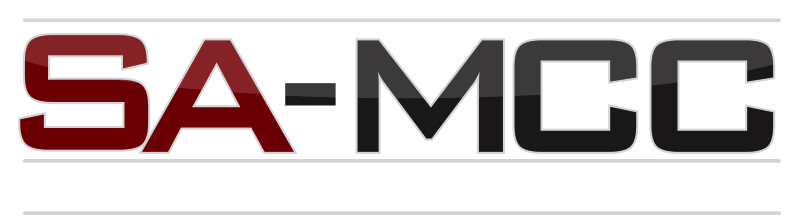
SA-MCCTM was developed to satisfy the various application needs of our customers. SA-MCC Multiple Complex Overlays can be custom blended to provide material characteristics needed for specific wear resistivity. For example, if the application requires increased impact resistance and temperature rating, the blend of complex carbides would have higher levels of Molybdenum and Niobium.
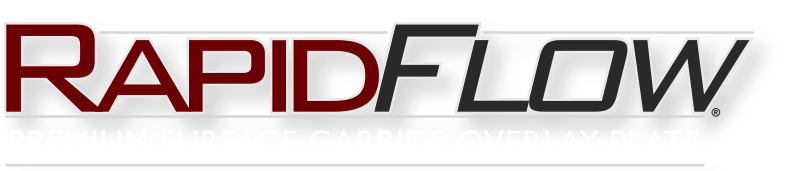
SAS Global Engineers a smooth surface finish on all SureAlloy® Premium Weld Overlay Products. The standard SureAlloy® surface finish can be blanchard ground to provide an even lower coefficient of friction for applications with heavy material hang-up issues. This premium surface is known as RapidFlow® Premium Surface Carbide Overlay Plate. The surface is ground and polished to a 0.2 Ra Micro-Meters finish. This finish is smoother than a stainless steel 304 with 2B finish.
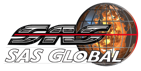
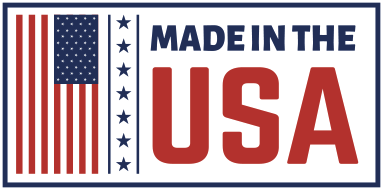
Copyright © 2024 SAS Global Corporation | All Rights Reserved